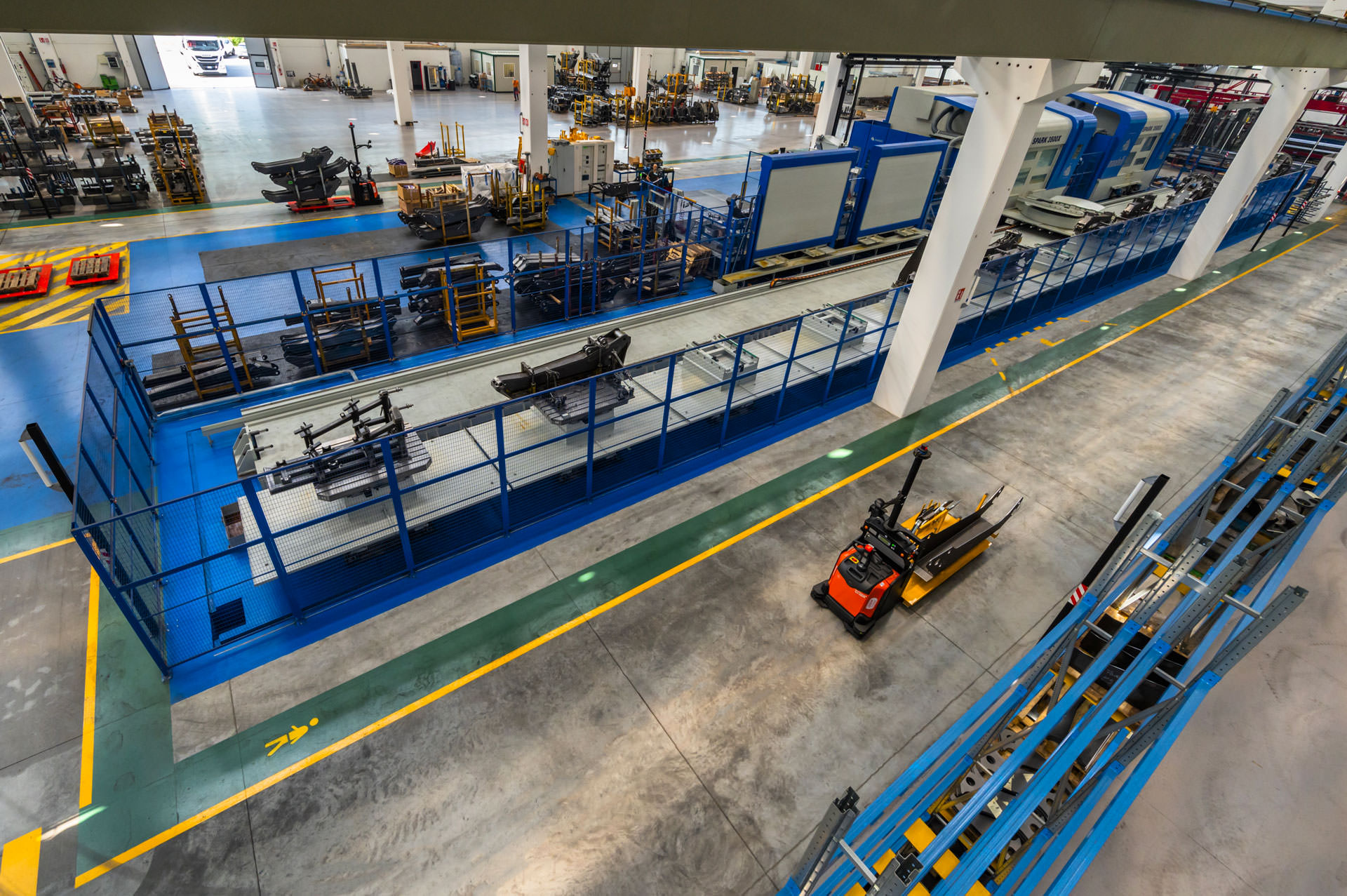
Fassi is growing as a network and a group not only in the world, but above all in the territory where it was founded: the Bergamo area, where nowadays 5 out of its 6 Italian-based companies are located.
In fact, a new Carmo production plant will be soon fully operational in the town of Nembro. Carmo is a Fassi Group company founded in 1975 and specialises in the production of medium-light cranes and in mechanical and metal work production. The production area was doubled in 1996 with the addition of 6,000 square metres. Today, a new 17,000 square-metre production plant joins Carmo, which houses machinery that mostly has automatised innovative technology that perfectly complies with 4.0 production systems. In fact, half of this €20 million investment was allocated for new machinery. Machining centres, laser cutting machines and welding robots now complete the group’s new factory. As a result, Fassi is even more oriented towards the evolution of production processes, achieved by connecting the plants and managing production in a more flexible way.
This is an essential activity, given that Fassi internally produces 90% of the 45 families of cranes. The cranes are globally available in 50,000 different versions, each of them composed of many parts and specific and differentiable components.
This is a fundamental step in making the world of Fassi products more competitive and in always being able to guarantee a wide range of choice, since the number of available crane versions is so large.
Eugenio Sarzilla, President of Carmo
How and when did the need arise to create a new Carmo in line with digitalisation and build such an important expansion?
In all respects, Carmo can be considered the beating heart of Fassi because it is here that the raw materials arrive and is where the steel plates are handled and treated. At the end of processing, the pre-assembled parts leave Carmo, ready to be painted. This step involves Carmo for medium-light cranes and Omefa for the heavy ones.
In the previous facility, production needs created a large stock of materials that made it difficult to move parts around, especially because the market is trending towards increasingly larger cutting machines. Also, some machinery was in need of renovation.
Today Carmo is a 17,000 square-metre facility. What is the added valued of this programme?
Nowadays there are two Carmo facilities: the one for metal working takes care of parts manufacture; the other handles the painting process, assembly and medium-light crane testing.
The expansion to 17,000 square metres has led to a technological refurbishment where mechanical and metal work production are concerned. It is an operation aimed at achieving high-quality production standards and great production flexibility thanks to its pioneering machinery.
Flexibility is fundamental in satisfying the various needs of the market and in progressively modifying production plans.
How is the “new Carmo” structured?
The operation involves the whole supply chain: from handling steel plates, to cutting, welding, logistics, mechanical production up to the machining centres. The welding process had already been revised.
Today the process of handling and cutting steel plates is an integrated system, so once the steel plate is positioned at the top of the machine by the operator, it is picked up onto a rack and positioned in the sandblaster. Afterwards, it enters the suction cup system directly from the cutting machine, and manages and supervises two lasers, both during loading and unloading. Once the steel plate is cut, it is picked up and inserted into storage areas and then taken out according to priority.
When the work of the cutting machine is done, the parts are sent to the first welding stage and directed to the different implementation programmes. The welding stations today are particularly advanced and so the operators receive all the features of the product directly at their workplaces and the entire logistics are entrusted to autonomous forklifts or shuttles that that load and unload the different workstations.
This automation system has allowed us to transform our logistics hub as if it were a “zero-miles” premises because we have managed to internalise many of the operations.
The new devices for mechanical production have been another important game-changer. In fact, we have an FMS with two twins machining centers with 200+200 tools server by a shuttle and controlled by a PC supervisor.
Speaking of the work force, how many people work in Carmo?
There are 40 operators in 3 shifts. Luckily, we have a lot of space and this allows us to work safely. Distancing between workers is guaranteed, together with constant cleaning and sanitation of the workplace.
New spaces, investments in digitalisation and automation. What will be the practical advantages of this investment?
There will certainly be an increase in productivity in terms of the cutting phase, benefits and advancements for the welding process and a significant improvement and increase in mechanical production. Not to mention the flexibility that I discussed before. There are so many Fassi cranes and each crane has different models, each one of them with different code numbers. By code, I mean part types. Thanks to an automatised system, it is possible to handle requests for new codes quickly and therefore to produce new parts.
Given the huge amount of innovation and technology, training will also play an important role…
Definitely. Our employees always receive specific training on the machinery they are using. Operators are requested to study the machinery in great detail and even to attend seminars directly at the companies that supply that machinery. Training is continuous and always specific.
When will the new Carmo site be fully operational?
We began moving to the new plant on 27th December 2018. The relocation was completed at the end of 2019 without stopping production or work. We are 90% functional now. We soon hope to be at 100%.